A History of Ion Implantation
Particle Accelerators and Ion Implantation Technology
In 1956, particle accelerators were being used for nuclear physics research. The largest accelerators had a terminal voltage of 15MV and weighed more than 200 tons. Each consisted of an ion source, an acceleration section, an analysis magnet, and a target chamber. The first small research ion accelerator was built by High Voltage Energy Corporation. It was 30 feet long and delivered 20 microamperes of argon ions at 100keV, with a hollow cube holding four 1” wafers as a target area. It was this project that spurred the idea of ion implanters designed for production purposes. Initial interest in ion implantation for doping purposes was for it’s ability to greatly increase the yield of MOS transistors which were being used in digital hand-held calculators. Before the ion implanter, doping was achieved by diffusion, but with this process turn on voltage of the transistors produced varied and required sorting, with high fallout. Ion implantation allowed control of the threshold voltage, adding direct and precise control over the dopant dose, and thereby drastically increased yield. The introduction of the modern DRAM cell and the microprocessor in 1968 and 1971, respectively created a dramatic change in the electronics industry.
Peter H Rose - An Ion Implanter Pioneer
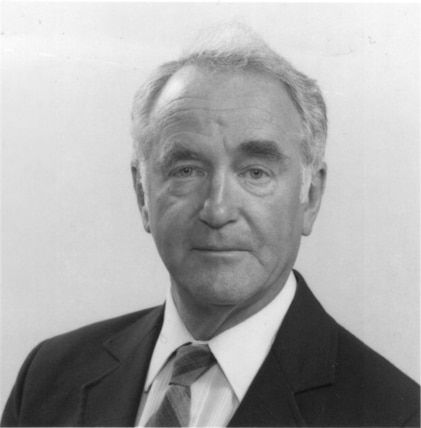
Peter H Rose was the first person to envision robust ion implanters for production purposes, easy to use with high through-put and atomated wafer handling.
Rose’s business, Extrion, first appeared publicly at the 2nd Conference on Ion Implantation in Semiconductors in Germany, May 1971. After just 18 months in business, the first machine was delivered to National Semiconductor, an Extrion 200-DF4.
Until 1971, the typical device was about 10 micron and wafers were handles with tweezers. The earliest automated wafer holder was a ring that held 200 2 inch wafers hand mounted to thin aluminum platen.
Nova is funded by Cutler Hammer, who is eventually purchased by Eaton along with Kasper, in Austin, TX, and Eaton Semiconductor Equipment Operations is formed.
NV-10-60s start shipping in 1979; these implanters were revolutionary, featuring sliding seal technology, bi-directional mechanical scanning, superb dose uniformity, cooled discs, and simple operation. Exchange arms were used to achieve throughput, which was important because wafers were still being hand loaded onto the disks. A dosimetry slot in the disk provided real time dosing control. The concept of the slot disk was carried forward and is still being used today in GSD, Ultra and Paradigm implanters.
By 1975, wafers were individually unmounted and drawn by gravity, moving through single wafer vacuum locks in and out of the implant beam.
In 1976, Peter Rose/Extrion briefly joined funding partner Varian, as Varian entered the semiconductor market. Varian declined to fund a new type of implanter, a high current machine to be used for new applications such as source/drain doping.
In 1978 Peter Rose joined Nova Associates (later acquired by Eaton and spun off as Axcelis), founded with the goal of producing the world’s first high current production implantation system.
Ion Implantation Innovation in the 80s
Through out the 80s, the industry saw amazing innovation. In 1981, we saw the introduction of the Nv-10-80, which raised the energy level to 80 keV. The NV-3206 was the first 150mm tool.
In less than a decade datalock is introduced, as well as automated loading processes. Single charged energy went from 80keV to 160keV. LINAC based acceleration is added to commercial semiconductor manufacturing. Oxygen implantation is introduced, bringing on commercial SOI production. istributed control systems are developed. Applied Materials entered into the high current market place.
Advancements in the Semiconductor Industry During the 90s
In the decade that followed, the 90s, we began to see things like two-axis tilt capable gyroscopic end stations, which could handle advanced processes and a throughput greater than 200wph. Wafer handling platen designs are introduced, allowing rotation during processing and multiple tilt angles. In situ particle control monitors and change monitors become standard use. Beam purity improves. The industry begins to work on production, to focus on performance, quick species changes, and high beam utilization.
In the mid 90s, integration of wafer handling advances and the reliable nature of LINAC technology spurred high energy growth, as high energy isolation techniques became commonplace at reasonable CoO. Back biased Secondary Electron Flood (SEF) is introduced to provide charge control with low high primary electron emission risk. By the end of the 90s, the stage was set for remote diagnostic systems.
Key Semiconductor Industry Innovations in the 2000s
In the early 2000s, the focus was on improved design, changes that brought extended source life, low cost of operation, productivity, and reliability. Framework is provided for electronic diagnostics and advanced process controls. 300mm implanters become available for application requirements that are beyond 100 nanometers. There was an expanding range of applications in sub-65nm generation device manufacturing. Unprecedented beam currents and performance levels are brought to the high dose space. Single wafer high energy ion implantation is in full production swing.
In 2013, a 12-stage LINAC with energies up to 4.5 MeV is introduced, as are scanned-spot-beam architecture and five filter beamline designs. In 2016, the 12-stage LINAC would see energies up to 5.25MeV. By 2017, 14-stage LINAC offered extended multiple charge capabilities and delivered energies up to 8 MeV.
Ion Implantation Today
As the market has matured, it has become ever more specialized. Dual LINAC designs for energies up to 15 MeV have been introduced within the last 5 years. Low energy, high dose supports leading edge applications. High energy, high current is needed in the power device market. Aluminum implantation is used for high volume power devices, a market that also required unique features and process control such as silicon, thin silicon and silicon carbide capabilities. Active pre-heat and post cool stations have been developed SiC processes that can get up to 650 C. It is possible to achieve more than a dozen configurations across multiple product backbones.
Ion implantation is integral to integrated circuit manufacturing. As the complexity of chips has grown, so has the number of implant steps. Today, a CMOS integrated circuit with embedded memory may require up to 60 implants.
There are four types of implant systems common in the industry. Three of these are line-of-sight beam line systems: high-current (for low-energy and/or high-dose applications); medium-current (for lower doses); high-energy (for very deep implants). The fourth uses plasma doping for applications requiring exceptionally high doses or conformal doping of regions that cannot be reached with the line-of-sight beam line systems (e.g., sidewall doping in three-dimensional fin field effect transistors). These systems deliver leading-edge beam angle control, dose control, uniformity, and wafer-to-wafer repeatability.