Additional Manufacturing Processes
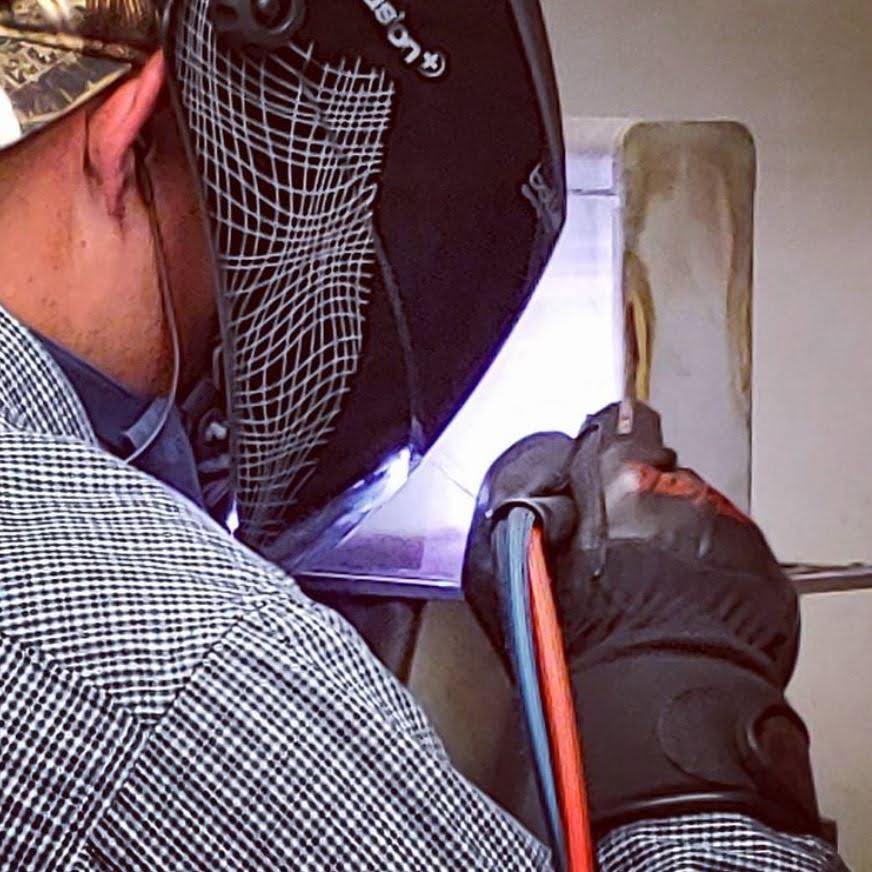
To function as a turnkey precision CNC machine shop, having expertise in a broad range of manufacturing processes is essential.
- Grinding
- Heat Treating
- Arc Welding
- Plating
- Coatings and Paints
- Surface Finish
- Passivation
- Brazing
- Epoxies and Resins
- Vacuum Brazing
- Dip Brazing
- Soldering
- Vapor Degreasing
- Ceramic to Metal Sealing
- Electropolishing
- Production Leak Testing
- Pressure Testing
- Part Marking
Processes Overview
Grinding is a very useful technique for metal removal at fast rates and for high level finishing of final products. The advantage of using such a process over conventional metal removal processes are the rate of removal, surface finish, ability to remove metal from a hardened surface, and low pressure material removal.
Heat treating refers to the controlled process of heating and cooling a material to improve its properties, performance, and strength. The importance of heat treatment is evident in many products in the automotive, aerospace, construction, agriculture, mining, and consumer goods industries, all using heat treatment to improve the properties of materials. The heat treatment process can be applied to ferrous metals such as cast-iron, AHSS, stainless steel and other alloy steels, as well as non-ferrous metals such as aluminum, magnesium, titanium, copper, or brass.
Arc Welding is a fabrication process whereby two or more parts are fused together by means of heat forming a join as the parts cool. Arc welding is a fusion welding process in which coalescence of the metals is achieved by the heat from an electric arc between an electrode and the work. Electric energy from the arc produces temperatures ~ 10,000 F (5500 C), hot enough to melt any metal. Most AW processes add filler metal to increase volume and strength of weld joint.
Plating is a manufacturing process in which a thin layer of metal coats a substrate. Metal plating provides many benefits to products made from metal and other materials. Plating can produce improved corrosion resistance, increased solderability, enhanced hardness, reduced friction, altered conductivity, enhanced paint adhesion, material deposition and increased magnetism.
Coatings and Paints provide more than just an aesthetic finish to on industrial equipment or base materials. Industrial coatings are engineered barriers that protect parts from a wide variety of damages and extreme environments. Different coating materials can protect parts from heavy wear, physical impact damage, and/or heat and fire and repel dirt, grease, and contaminants with a nonporous topcoat.
Surface Finish as a process alters the surface appearance of a workpiece by performing different actions that can reshape, remove, or add to the final product. There are many benefits that can be achieved with surfacing finishing, such as improving the product’s appearance, increasing lifetime, improving resistance to corrosion, increasing chemical resistance, increasing the strength of the material, prep for paint/coatings, improved electrical conduction, reduction of friction, improved resistance to wear, increase of surface area.
Passivation is a widely used metal finishing process to prevent corrosion. In stainless steel, the passivation process uses nitric acid or citric acid to remove free iron from the surface. The chemical treatment leads to a protective oxide layer that is less likely to chemically react with air and cause corrosion. Passivated stainless steel resists rust.
Brazing joins parts by heating them to more than 840°F and applying a filler metal that has a melting temperature below that of the base metal. Filler metal flows into the joint by capillary attraction. Brazing has several advantages. Dissimilar metals can be joined.
Assemblies can be brazed in a stress-free condition, and complex assemblies can be brazed in several steps by using filler metals with progressively lower melting temperatures. Materials of different thicknesses can be joined, as can cast and wrought metals. Nonmetals can be joined to metals when the nonmetal is coated. Metallurgical properties of base materials are not seriously disturbed, and brazed joints require little or no finishing.
Epoxies and resins offer very good adhesion properties, high adaptability, low shrinkage, high strength, resistance to corrosive liquids and environments, good electrical properties, reliable performance at high temperatures, and adhesion to various substrates.
Vacuum Brazing is a manufacturing process for joining components by heating a braze alloy between the assembly components. Assembled parts are kept fixtured together to maintain contact during heating and cooling. Assemblies are placed in a vacuum furnace that is heated to at least 450°C, a level that will melt the braze alloy but not the main material. The furnace has a vacuum environment, which eliminates the risk of oxidation and need for flux.
The molten braze alloy fills in gaps between components through capillary action so that when the part is cooled, it forms a joint through atomic attraction and diffusion. Vacuum brazing produces a clean, one-piece construction with strong joints with thermal conductivity nearly the same as the parent material. Uniform heating, tight temperature control, no post cleaning processes, and process repeatability make Vacuum brazing an ideal process for thermal and structural assemblies.
Dip Brazing can be used on a variety of metals including steel, copper, brass, and bronze which are often brazed with copper phosphorus silver alloys. Dip brazing is a cost-effective option for parts assembly and large brazing furnaces allow for mass production of items such as electronic devices, medical equipment, and fixtures for the military. Aluminum is very well-suited for the brazing process and provides reliable, high-quality results. Assembly design is a crucial consideration as it can affect heat transfer ability, filler flow, if a fixture is needed, length of braze, and assembly procedure. Aluminum dip brazing is particularly excellent in applications such as chassis, aircraft parts, enclosures, heat-exchangers, and air-cooled applications.
Soldering is a joining process used to join different types of metals together by melting solder. There are three types of soldering which use increasingly higher temperatures, which in turn produce progressively stronger joints.
The soft soldering (90 °C – 450 °C) process has the lowest filler metal melting point of all the soldering types at less than around 400°C these filler metals are usually alloys, often containing lead with liquidus temperatures under 350°C. Because of the low temperatures used in soft soldering it thermally stresses components the least but does not make strong joints and is then therefore unsuitable for mechanical load-bearing applications. It is also not suited for high temperature use as this type of solder loses strength and melts.
In hard (silver) soldering (>450 °C) brass or silver is the bonding metal used in this process and requires a blowtorch to achieve the temperatures at which the solder metals.
Brazing (>450 °C) soldering uses a metal with a much higher melting point than those used in hard and soft soldering. However, similarly to hard soldering, the metal being bonded is heated as opposed to being melted. Once both the materials are heated sufficiently, you can then place the soldering metal between them which melts and acts as a bonding agent.
Vapor degreasing is the cleaning process of choice for providing parts free of contamination. It is a commonly used cleaning method because it is both simple and effective. Vapor degreasing is both extremely effective and convenient for removing metalworking fluids, cutting oils, corrosion inhibitors, and waxes – soils that commonly remain after parts manufacturing at OEM and MRO (maintenance, repair, and overhaul) facilities.
Ceramic to metal sealing is a well-established process that requires a metallization layer applied on the ceramic and then secondarily brazing the metallized ceramic and the metal component together using a braze (or solder).
Electropolishing is an electrochemical process that removes material from a metallic workpiece, reducing the surface roughness by levelling micro-peaks and valleys, improving the surface finish. Electropolishing is often compared to, but distinctly different from, electrochemical machining. It is used to polish, passivate, and deburr metal parts. It is often described as the reverse of electroplating. It may be used in lieu of abrasive fine polishing in microstructural preparation.
Production leak testing is implemented to verify the integrity of a manufactured part. It can involve 100% testing or sample inspection. Because manufacturing processes and materials are not “perfect,” leak testing is often implemented as a final inspection step to verify integrity of a product.
Pressure Testing is a non-destructive test performed to ensure the integrity of the pressure shell of a product to ensure it is capable of safely withstanding its rated pressure and is leak tight.
Part Marking involves creating of permanent markings on parts surfaces. In many industries, the most common identification forms include QR codes, serial numbers, and data matrix codes.
Since 1984
We are proud to support our local communities with jobs that offer good working environment, excellent pay and benefits, growth opportunities and stability. Proud to be an American Manufacturer and a Woman Owned Business.
Contact Us Today